Here is a knife made by Brett. I really love the antler handle! It is O1 tool steel, stainless steel pins, and elk antler handle.
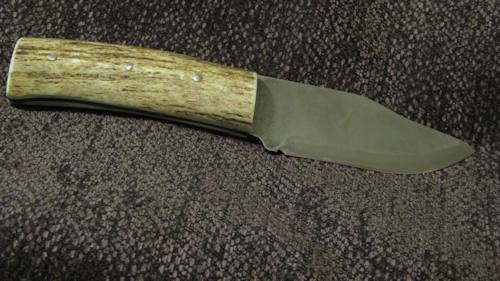
He also made a sheath for this knife:
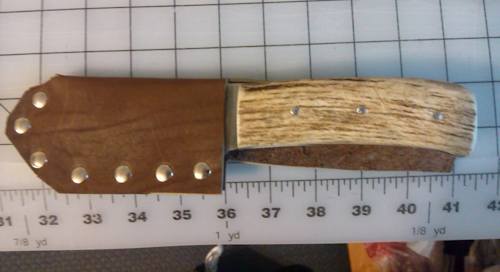
Here is a karambit made by Wes. He makes custom knives and you can check them out on his website here. Here is what he has to say about this knife:
Lilith is the sister blade to my Demon Tooth, it is made from 1095 high carbon steel in 1/8th thickness. Oil quenched, and tempered. Grip material is a durable resin type material that takes a bright Chrystal looking appearance when polished. Blade is 6.5 inches long grip is 4.5 inches long for a total of 11 inches overall. The Blade is covered in fire scale to give it an evil appearance.
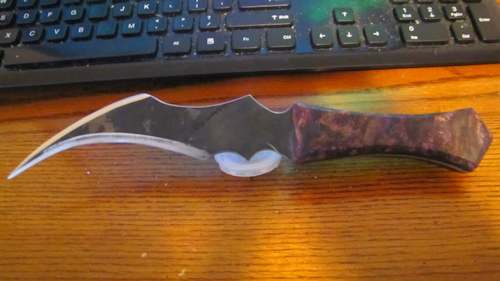
Here is a karambit made by Olve. Wow, that is one serious fighting knife and it came out great. My thanks go to him for sending in the picture. You can see the tutorial on how to make a karambit here.
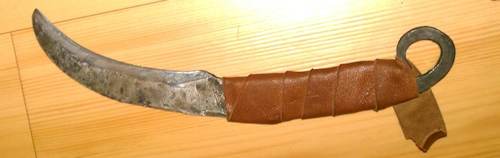
Here is a push knife made by Connor. It came out great and my thanks go to him for sending in the picture. The tutorial for making a push knife is here.
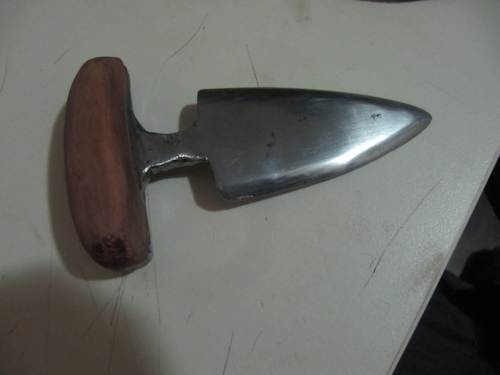
And Connor made a mount to display it on. I like it!
Here is a knife James made by following my tutorial. He made it for his son. He used O1 steel with Bokoto wood and put metal pegs in the handle along with a lanyard hole. He shares a tip with us about drilling for the pegs:
" When I dry fitted the pins to the tang and handle I had trouble with getting them to fit. There isn't much tolerance and they weren't going in all the way even after I sanded the burrs. I'm sure this is because I didn't use a drill press and was not completely straight when drilling. So I placed the pins in the freezer which reduced them temporarily just enough to allow them to slip through nicely."
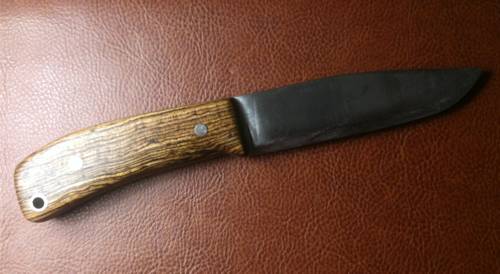
Here is a knife made by Asmon. He used my template and it looks terrific! He will send another picture when it is done! My thanks go to him for sharing this with us. Asmon also came up with some great do's and don'ts of knife making
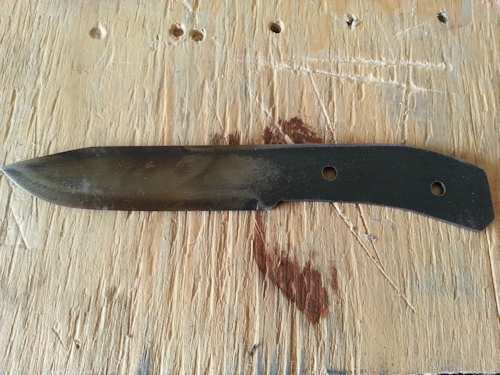
And here is the fnished knife:
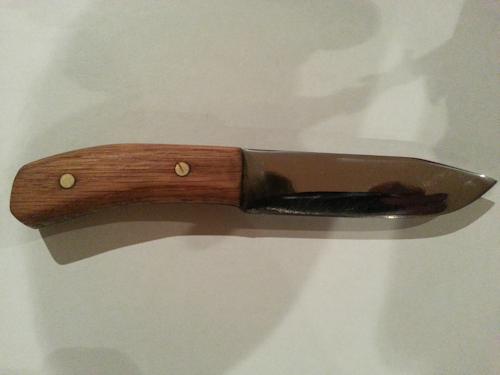
Here is a knife made by Michael. He made this out of an old lawnmower blade. And he used common hand tools. He did a great job and did it without a forge or anvil! And he is only 15 years old!
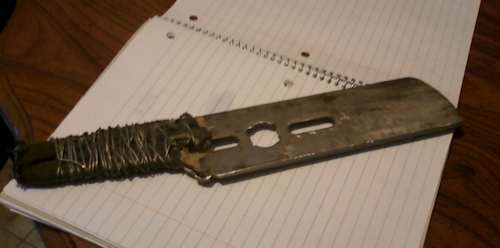
Here is a knife made by Andrew. It came out great! And he is 13 years old!
Here is the first knife made by JJ. It is coming along great. Pretty terrific knife considering JJ is only 14.
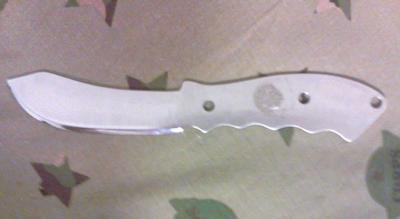
Here is a terrific knife made by Edward. It has a great shape and look to it. Here is what he has to say about it:
. This is the first knife I've ever made. The blade i cut from a big saw blade i got from a saw mill. The handle i cut out of a blonde cedar tree.
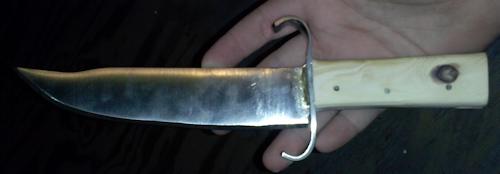
And here is the completed knife: He decided to change the handle to red mahogany and stained it red mahogany to get it deeper and richer.
Here are three knives made by Christopher. My thanks go to him for sending in the pictures. And he tells us how he made them. These are a great example of what you can make without forging.
The handle material is, on the top picture is just 1/8" cord wrapped around the tang of the dagger. in the middle picture the handle of the knife is soft leather wrapped around the tang. in the bottom photo, the handle of that wicked looking knife the handle is denim.
All of the knifes and swords that I make start as a flat bar of steel, (either 3/16 or 1/8 inch thick,) then I cut out the rough shape, file down the extra bits and then I bevel the edges, then I make the handle, put it on, sharpen the blade, and it is done. By the way when I make a very un-straight tang I just hamer it out straight. And yes the steel is cold when I do that.
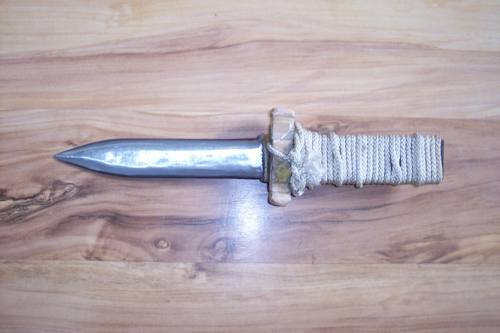
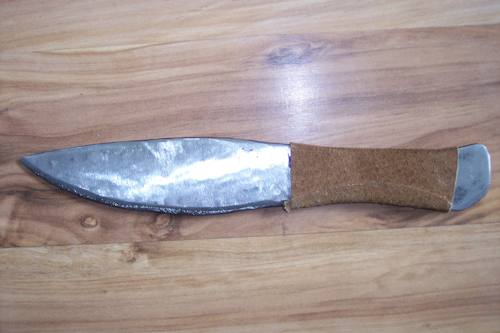
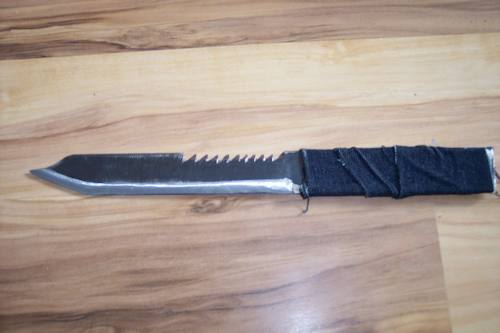
Here is a knife made by Kevin. I love the look and shape of this knife. My thanks go to him for sending in the pic.
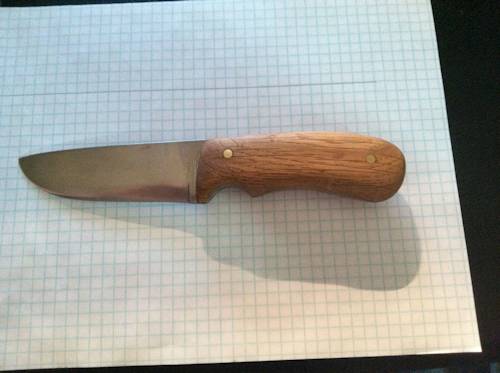
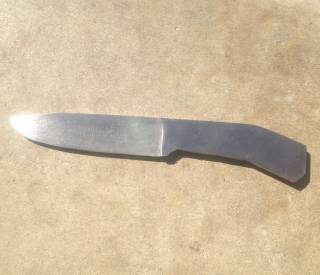
Can you make a knife using the method I have here? You sure can! Here is one made by John Graham. It looks great. He has since completed it. And my thanks go to him for sending in the pic.
Want to give this tutorial a try? You can do it and you can have some fun with it too! Come up with your own knife design! This is exactly what 4xdblack did! Here is a picture of his knife. It is almost ready for the handle. My thanks to 4xdblack for sending in the pic!
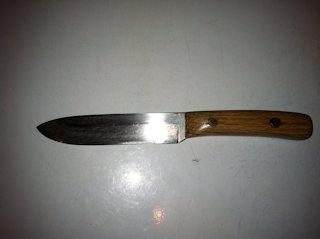
And here is a knife made by Scott using this tutorial. My thanks go to him for sending in the pic. All that remains is to polish the handle and sharpen the blade.
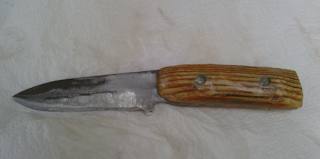
And here is a knife made by John H. using the stock removal method. I love the grain of the wood and my thanks go to him for sending in the pic!
He made it out of an old Lawnmower blade and some Lightered wood.
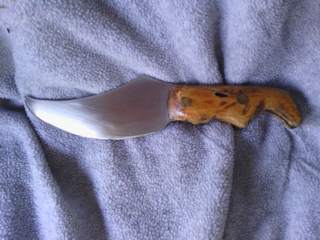
Here is another knife made by John H. This is the Eagle! Wow, I love the shape of both the blade and the handle.
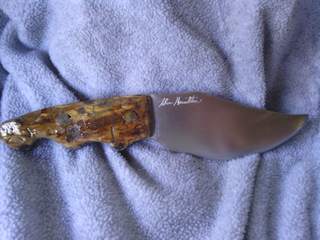
And this one is the rugged woodsman. John is developing a real feeling for the aesthetics of knives!
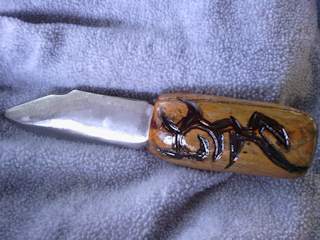
And here is a tribal boot knife made by John.
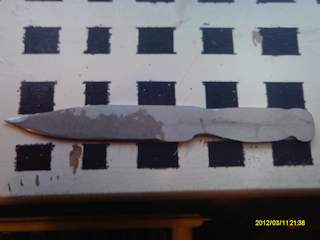
And here is a knife that Jean-Luc is making. All of the work was done on a bench grinder. He will be attaching a Yew handle and adding serrations to the top near the handle. Can't wait to see how it comes out!
Ok! Jean-Luc has finished his knife! Here are three pictures of it!!
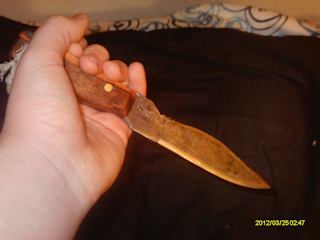
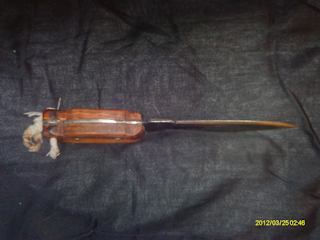
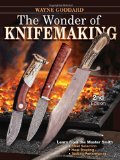
The Wonder of Knifemaking
Master smith Wayne Goddard is an icon in the field of knife making. As a full-time maker, teacher and writer, Goddard works as hard to teach knife making skills as he does to acquire them. His affiliation with BLADE Magazine has brought new and interesting information, tips and tricks to thousands of would-be knife makers. Other popular titles from Goddard include The Wonder of Knifemaking (2000) and $50 Knife Shop (2001 and 2006).
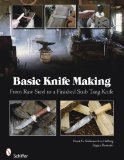
Basic Knife Making: From Raw Steel to a Finished Stub Tang Knife Learn the craft of knifemaking. 205 color images and step-by-step instructions provide for all stages of construction, from selection of the steel, to forging the blade, assembling the handle, and constructing a holder.
|